Client Alert
Looking Around the Corner: Prepare for Increasing FDA Oversight and Review
August 02, 2021
By Peter V. Lindsay
Since the beginning of the COVID-19 pandemic, FDA inspections have been a moving target. The Food and Drug Administration (FDA) first paused inspections before announcing last summer it would resume “mission critical” inspections and certain prioritized domestic inspections, where possible based on a risk-based assessment tool. Despite these efforts, the pandemic significantly decreased the number of inspections—so much so that in January 2021, the GAO raised significant concerns about a growing inspection backlog.
As vaccine distribution increased and COVID-19 cases generally declined in the Spring, the FDA issued its “Resiliency Roadmap,” in which it anticipated the resumption of more surveillance inspections of U.S. facilities by mid-Summer. And in July 2021, Acting FDA Commissioner Janet Woodcock announced that the FDA had begun transitioning back to standard operations for domestic inspections. She also confirmed that the FDA would still conduct mission-critical inspections for ex-U.S. facilities. According to the Resiliency Roadmap, routine surveillance inspections for ex-U.S. facilities (at least those using U.S. staff) are not expected to resume until later this year at the earliest.
Although the FDA has increasingly used monitoring tools other than in-person inspections, including record requests and product sampling at the border, it is clear that Congress and others are pressing the Agency to find ways to increase its oversight and monitoring over the coming year. In fact, the FDA has budgeted for a dramatic increase in inspections, both domestic and ex-U.S., for FY22, to levels actually exceeding those conducted pre-pandemic. While virus variants make precise predictions difficult, the FDA clearly feels the pressure to increase oversight and monitoring and with an eye toward resuming in-person inspections as soon as feasible. Life sciences companies subject to FDA jurisdiction need to think about their readiness for this planned increase in compliance surveillance.
In addition to standard preparation plans, companies should consider the following:
- COVID-19 Guidance and Response: the FDA recognized that the COVID pandemic may have led to companies delaying, reducing, or otherwise modifying activities under their Quality Systems to maintain production and drug supply. The FDA cautioned that manufacturers should carefully review and document the impact of such deviations using a risk-based approach. Risk assessments and any interim or remedial steps are likely to receive additional review, and documentation should be carefully reviewed for thoroughness and rigor. Such pre‑review is particularly important for any risk assessments associated with critical process or product deviations.
- Quality System Trends: In most cases, the pandemic will have introduced a longer‑than‑normal inspection cycle for a particular facility. That longer cycle will mean a more extensive record for review during a records request or an in-person inspection. Careful attention will be needed for quality records, especially for significant (or delayed or overdue) complaints, deviations, and CAPAs. Trends may have shifted during the pandemic, and Companies should be prepared to explain whether shifts reflect changes in true quality indicators or if other variables help explain the metrics. The quality and rigor of deviation and complaint investigations also should be assessed to ensure these processes reflect appropriate efficacy and evaluation of root cause during review by regulatory authorities. The FDA may pay particular attention to resource levels as commercial activity may have varied from historical measures, either higher or lower.
Companies also should pay close attention to episodic or adverse trends in other areas, for example in environmental monitoring, that may raise questions about the effectiveness of a facility’s CAPAs in that area. Management will also want to review training and qualification metrics as training programs may have faced challenges in completing scheduled tasks.
- Supplier Management: Significant attention has been focused on the FDA’s ability to conduct in-person inspections, and in many cases, companies have faced similar challenges conducting effective supplier audits. These audits have also been postponed, handled as a “paper” review, or in some cases, some form of remote audit has occurred. Although the FDA is likely to appreciate the need to deviate from supplier management procedures, companies should review their documentation (both for the activity itself as well as any pandemic-driven accommodations) and associated risk assessments for these arrangements. These alternative audit approaches may have limitations, and management needs to think carefully about whether supplier monitoring tools have been sufficient or could be enhanced further before the FDA undertakes its review.
Current circumstances present a good opportunity to review the effectiveness of supplier management programs. The FDA has encouraged manufacturers to proactively obtain information from suppliers about the impact of COVID-19 on their operations and any changes made that could impact the quality of the finished product. Some changes may be quite apparent, but others, including changes in Quality System implementation and oversight, may be more subtle and only manifest themselves over an extended period. Careful assessment of the supplier management processes will not only help in inspection readiness (as the FDA is increasingly focused on supply chain quality management) but may help to refocus these programs on the most effective tools for maintaining consistent, quality supply.
- Data Management Controls: With the pandemic and other factors leading to increasing levels of automation, and with companies using increased levels of remote supervision and data reviews, it is a good time to review the implementation and execution of data management controls, including access controls, data and audit trail reviews, and related training.
- Escalation of Significant Issues: Many companies have formalized policies for employees to bring significant issues to management attention. For effective execution, these policies frequently rely on informal communication and engagement that may have been impacted or modified during the pandemic. It is important for companies to assess whether these impacts or modifications continue going forward and how any changes affect the escalation processes and the broader quality culture. With potentially modified processes as a result of the pandemic, companies also need to be attuned to any new or different baseline feedback raising GxP issues in hotline or employee complaints.
- Positive Compliance Diligence: Current circumstances also present an opportunity, as facts warrant, to demonstrate good corporate citizenship through documented compliance efforts. Many life sciences companies took additional steps during the pandemic to ensure the effective operation of quality systems as extraordinary measures were implemented to address particular needs as a result of the pandemic and related changes to operations. Now is a good time to ensure that these activities can be presented positively to regulatory authorities, in an organized manner, and with appropriate documentation.
- Inspection Readiness: Many companies have responded to record requests, and some have participated in remote interactive evaluations or audits by various regulatory authorities. While these alternative types of reviews have helped Quality teams develop new skills in working with regulators, other skills for responding to in-person audit requests may have not received much practice over the last year or two. This is even more likely for subject matter expert teams supporting in-person inspections, such as personnel in production, engineering, validation, and the QC laboratory.
In some cases, Quality unit personnel may have shifted toward increasingly remote approaches to oversight because of pandemic precautions. As companies prepare for upcoming in-person inspections, it will be important to re-engage with production and other groups to ensure that potential questions and issues are addressed in advance and not reviewed by the Quality Unit for the first time during an inspection.
Companies should evaluate, and consider additional inspection readiness activities, for these personnel who may have not interacted with the FDA for a prolonged period. Effective preparations often include focused third-party reviews to review information, identify effective presenters, and to keep subject matter expert teams well prepared for the expected increase in regulatory scrutiny.
Life sciences companies should be prepared to present to FDA reviewers, whether in person or remotely, their Quality System records, which may present a more extensive record than historically was the case and which may include unusual events or operations as a result of the pandemic. The upcoming increase in review as budgeted by FDA may also present an opportunity to demonstrate a company’s focus on regulatory compliance, even while coping with the extraordinary changes and challenges brought about by a pandemic.
Contributors
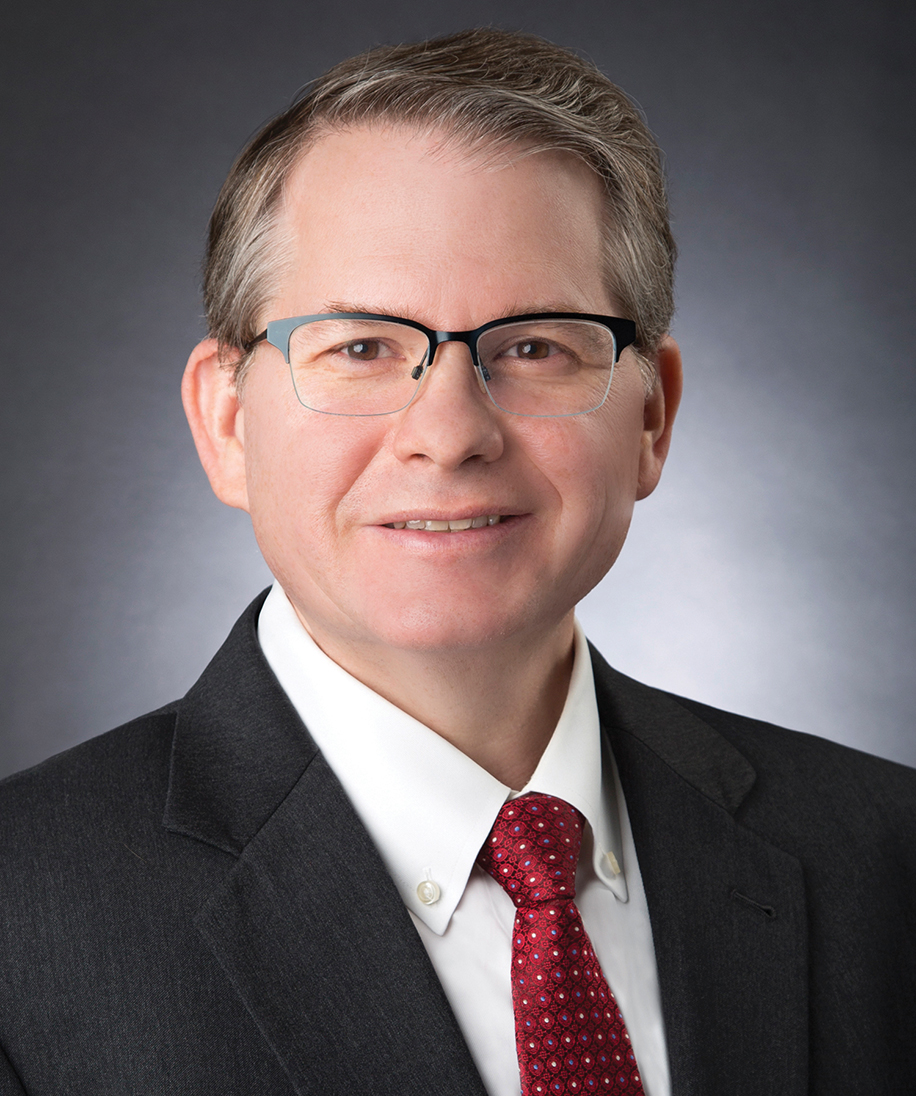